Introduction
In order to build better medical services and more efficiently Crash Cart Inventory Management, we recommend the deployment of Smart Crash Carts. If your budget is limited or you can manage to handle it at this time, there is no need to continue. However, if you want to build a modern digital hospital, improve the quality and efficiency of nursing care, increase the satisfaction of both physicians and patients, or reduce hospital operating costs, we recommend that you read this article deeply and consider investing in a smart Crash Cart.
What is Crash Cart Inventory Management?
Crash Cart Inventory Management refers to the periodic control and inventory management of the condition, chemicals, and equipment of crash carts by a specific person. crash carts, as the name implies, are indispensable equipment for rescuing a patient who has suddenly changed in an emergency. Thorough crash cart Inventory Management is important to demonstrate concern for patient life and to provide the most efficient and reliable medical services in emergency care. It is also an important indicator in rating hospitals and evaluating the quality of nursing and medical care.
The number of drugs and equipment in a crash cart varies slightly depending on the needs of each department and hospital, but typically a crash cart contains 20 to 30 drugs, 100 to 200 bottles, and 30 to 40 pieces of equipment. Depending on the size of the hospital and the number of departments, a typical hospital may have 5-10 Crash carts, while a general hospital may have 50 or more. Crash cart Inventory Management includes checking the type and quantity of drugs, whether they are properly stored and expired, whether the equipment has sufficient power, whether oxygen cylinders have enough remaining, whether the equipment is sterilized and within its expiration date, and whether all drugs and supplies are in their designated locations.
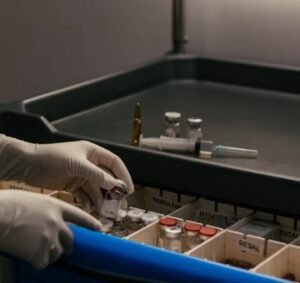
Frequency and Cost of Inventory Management
Crash cart Inventory Management frequency varies according to each hospital’s emergency response regulations, but most hospitals require to check crash carts for chemicals and equipment every shift, and a designated person is required to manage the carts and inspect them periodically. Following this frequency, it is a significant burden to check each and every item during the handover on each shift. As a reference example, if all medications and equipment were to be Inventory Managed by the nursing staff without outside interference, an average of approximately 25 minutes would be required per visit; three shifts per day would require a total of 75 minutes, and two inspections per week by dedicated staff would require 50 minutes per visit, for a weekly total of 75 minutes x 7 days = 525 minutes + 50 minutes = 575 minutes (9.58 hours).
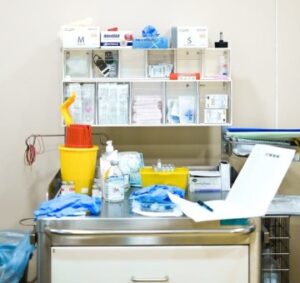
In other words, each crash cart requires more than 9 hours per week, so a hospital managing 20 carts would spend more than 180 hours per week, which, when converted to an 8-hour shift, requires enough manpower and time for one nurse to work 23 to 24 days. In terms of labor costs, 5,000 to 8,000 USD per month, or in some cases even more, is spent on Inventory Management. In order to reduce this cost, some have suggested simplifying management by using sealed stickers for infrequently used departments or introducing expiration date management using computerized tables, but even these have not solved the root of the problem. Although the burden of work has been shifted from the front office to the back office through the use of complex electronic charts, time and cost are still being consumed, and errors and omissions during Inventory Management have not been completely prevented.
Smart Crash Cart Inventory Management Method
To make the crash cart Inventory Management process more efficient and accurate, a Smart Crash Cart inventory management cart has been development.
The cart is equipped with a bar code scanner, infrared sensor, and RFID+ tags for rapid Inventory Management.
– Barcode scanner: By scanning the barcode when a drug is stored in the cart, information such as drug name, expiration date, lot number, manufacturer, and packaging quantity is automatically recorded in the system; a single scan is all that is required.
– Infrared sensors: Infrared sensors equipped on the carts will monitor the placement and take-out of goods in real time.
– RFID + Tags: Ultra-high frequency tags can be attached to drugs and equipments of any size, providing a clear picture of the status of all inventory. Simply by reading the tags on the items in the cart, the inventory status of all chemicals and equipment can be determined at a glance.
Combined, these features allow the quantity of items in a Crash cart to be constantly monitored, and the inventory status can be instantly checked by simply clicking on the cart’s smart screen during shifts and Crash cart Inventory Management. This improves efficiency and accuracy by avoiding manual checks, complex electronic charts, and identification problems due to worn labels on medications.
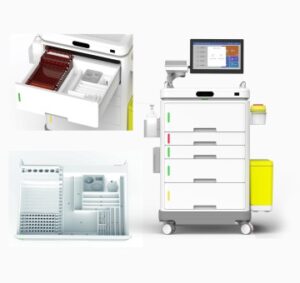
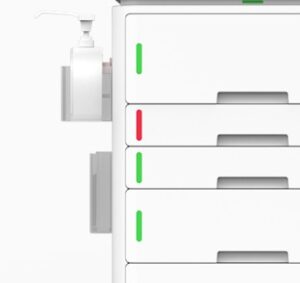
SUMMARY
In this era of declining population and labor shortages, hospital operations are changing as medical needs diversify and demands for medical services increase. Mechanical and repetitive tasks should be left to equipment, and healthcare workers are expected to focus on interpersonal tasks where human skills can be put to use.
Against this backdrop, it is recommended that all hospitals implement a Smart Crash Cart system to ensure the safety and smooth execution of emergency rescue operations. For further information or to discuss deployment, please contact us here.